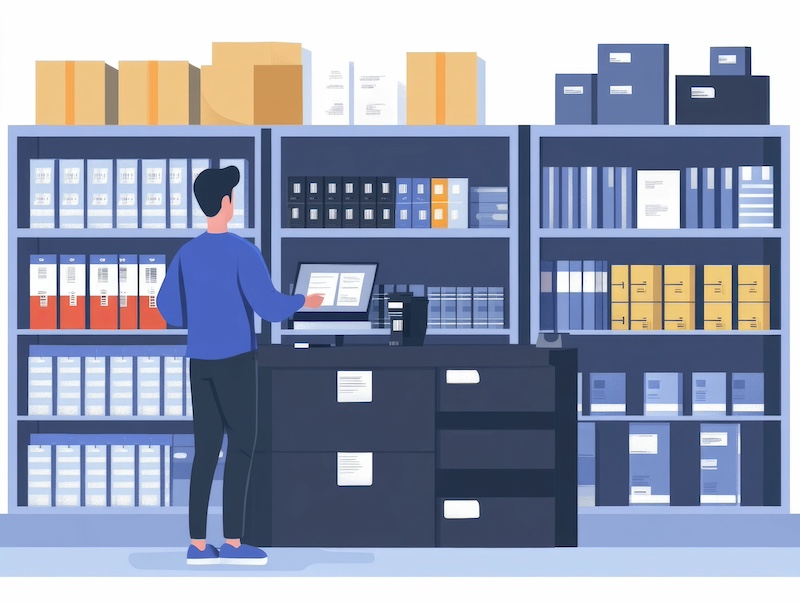
Operators of telescopic handlers are often manipulating multi-ton objects, often hundreds of feet above ground, on construction sites, roadwork or mines. When they are moving pieces of steel, palletized glass or iron ore, they must decide how to safely operate the machine’s boom without losing control of the load, or tipping, based on the lifting attachment and weight.
Telescopic handler technology company Magni offers its equipment with RFID technology and weight sensors to ensure that decision making is automated and accurate. A global company headquartered in Italy that opened a new facility in Kenilworth, N.J., in June, its equipment provides the lifting and support required for bridge and viaduct maintenance, large scale construction projects and mines.
Its latest accomplishment was restoration of the collapsed blades of Paris’ iconic Moulin Rouge Windmill before the Olympic Games.
Adjusting Up to 110,200 Pounds
Magni was founded by Ricardo Mani in 2013 and transitioned from a €24 million annual company to more than half a billion euro profit last year. The company boasts of its advanced, on-board technologies.
In fact, said Pietro Donati, the company’s marketing and communication director, RFID use is a differentiator. Many other companies that sell telehandlers require operators to go over paperwork to identify attachments and their requirements before they get to work.
Magni sells about 40 models of telehandlers managing heavy goods and equipment that range in weight from 6,600 pounds to 110,200 pounds. These telehandlers come with a Combi Touch Machine Management System and Live Load Diagrams to provide real-time digital data to operators on a screen in the cabin, as they go about their work.
Different attachments on the equipment affect what can be lifted and how. These attachments are optional according to projects for every Magni machine, said Donati. Identifying those attachments requires an RFID tag on each one, and a reader in the handler equipment boom. The company reports being the first such manufacturer to offer the RFID attachment recognition technology.
Its latest, Magni RTH 10.37 rotating telehandler, comes with a telescopic forklift and crane with multiple attachments used to lift goods over 100 feet. And it leverages a combination of weight sensors and RFID.
How it Works
Operators control the equipment from inside the enclosed cabin, which comes with touch screens to provide contextual information. For instance, the screens display camera images of the area around the vehicle.
The screens display mapping and flow charts to indicate how the boom can be safely manipulated based on the weight, height and angle, as well as the attachment on the boom, to ensure work is safe and effective.
First the attachment is connected to the boom for a specific operation. Different attachments can accomplish different processes. An RFID reader is incorporated into the boom head where attachments are connected. The reader is energized by wired connection to the battery-powered engine.
A passive RFID tag is welded to each attachment. Once the tag ID has been captured by the boom RFID reader, that data is processed in the system firmware. A weight sensor captures the weight of object being lifted, and that data is linked to the attachment ID, which results in a relevant display of parameters for moving that object safely without risking a tip.
The operator can view, for instance, that the attachment can handle two tons, and once that weight is captured, the system displays the five meters reach permitted for the boom and 50 meters of height authorized. As the boom moves, its location within that parameter is displayed on the screen.
Providing Additional Tags
The RFID tags and reader are designed to withstand the often wet and dirty outdoor environment.
Magni offers tagged attachments for use with its telehandlers, but it can replace the tags if they are damaged. If the tag breaks, users can indicate the attachment needing a new tag and Magni will program the tag linked to that attachment’s requirements and send it within a few days, said Donati.
All software is included in the machine and does not transmit to a cloud-based or on-premise system. The read data is not intended for record keeping. For instance, it does not track the specific attachment and how often or how it is used, Donati said, as that maintenance history is not required for the work being done.
“Its not like a tire that has to be changed after [a certain number] of miles,” he explained. “There is not this kind of consumption” of the attachment’s operational value.
App for Telehandler Management
Magni does offer an app to track the actual telehandler unit by sending GPS via GPRS to indicate where and how the equipment is being driven or operated and for how long.
In the meantime, if operators follow the instructions on their screen, “the risk of tipping is almost zero,” said Donati.
The technology saves time, he added, since operators don’t have to look up information on paper about the attachment and weight, height and extension limits.
‘People don’t want to be dealing with paperwork on a construction site or at a mine,” he pointed out
Alex Ha
tanhqYou Might Also Like
- Alex Ha
- 0 Comments